Комбікорм - це складна однорідна суміш очищених і подрібнених до необхідної крупності різних кормових засобів і мікродобавок, підвладна спеціальній обробці з метою підвищення її поживності, вироблювана за науково обгрунтованими рецептами і повністю забезпечує потребу тварин у поживних, мінеральних та біологічно активних речовинах. Залежно від виду вироблюваної продукції, яка, в свою чергу, призначена для певних видів і статевовікових груп тварин, на підприємствах застосовується єдиний технологічний процес виробництва комбікормів для основного дорослого поголів'я худоби, птиці та риб, а також комбікормів для поросят, телят і курчат 1 -4 днів.
Ефективність тваринництва і птахівництва в істотному ступені залежить від кормів. Збалансовані за складом корми, призначені певній групі тварин, є запорукою їх здоров'я і продуктивності і можуть повністю розкрити генетичний потенціал. Тому якісне виробництво комбікорму так необхідно, адже ринок м'яса, птиці, молочних продуктів, майже повністю складається з продукції дуже великих підприємств, які, для годівлі тварин і птахів, використовують комбікорми.
Технологічний процес виробництва комбікормів складається з наступних основних операцій: приймання, розміщення, зберігання сировини та передача його в переробку; очищення сировини від органічних, мінеральних і металомагнітних домішок; відділення оболонок від вівса і ячменю при виробництві деяких видів комбікормів; подрібнення очищеного сировини; контроль ( просіювання) подрібненої сировини; дозування і змішування компонентів; гранулювання.
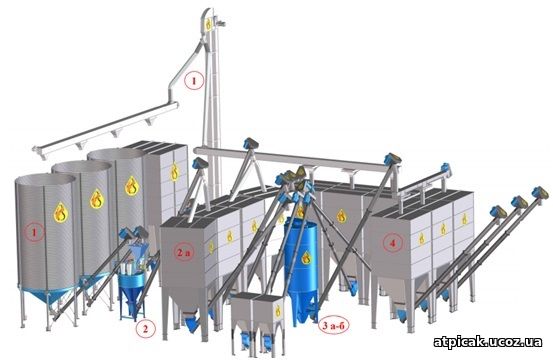
Рисунок 3.1. Загальний вигляд комбікормового заводу
Розглянемо ділянки та лінії виробництва по приготування комбікормів детальніше(рис3.1.).
1. Ділянка прийому та зберігання зернових компонентів, шротів:
Лінія може бути укомплектована ділянкою приготування преміксів.
- в нього входить власний горизонтальний змішувач 300-500 кг, встановлений на вагові датчики з текстовим дисплеєм;
- бункери для зберігання компонентів і готових преміксів;
- шнеки подачі і вивантаження.
- проектується і виготовляється відповідно до побажань замовника (кількість і ємність силосів, для зовнішнього або внутрішнього зберігання), з подачею на ділянку дроблення.
Комплектується транспортним устаткуванням:
- приймальний транспортер завальної ями;
- ковшова норія;
- розподільні транспортери із засувками по бункерах накопичувачів зернових компонентів і шротів.
2. Ділянка дроблення:
- може бути обладнаний установкою попереднього очищення циклонів типу, з камне- і металоуловлювачем.
Високопродуктивні дробарки для зернових і шротів, молоткового типу, продуктивністю до 7 тонн / год.
Максимальна споживана потужність 55 кВт.
2 а. Проміжне сховище подрібнених компонентів, що в свою чергу, дозволяє зробити запас вже подрібненого сировини перед ділянкою змішування і дозування.
Комплектується бункерами залежно від продуктивності кормоцеху від 5 до 15 тонн кожен.
3-а. Ділянка дозування - ваговій-дозуючий комп'ютер WDC25 дозволяє приготувати 40 сумішей з 30 компонентів;
- роз'єм підключення ПК і принтера;
- автоматична корекція при подальшому додаванні інгредієнтів;
- управління запасними компонентами;
- можливість програмування в кілограмах або в процентах;
- баланс споживання і витрати, контроль;
- програма на робочий тиждень;
- текстове програмування;
- вільне програмування вивантаження з підтримкою ПЛК;
- дозволяє одним натисканням кнопки переключити на інший рецепт.
3-б. Ділянка змішування - кормозмішувачі горизонтального і вертикального типу, об'ємом від 500 до 3000кг;
- висока точність змішування 1: 100 000, завдяки примусовій протипотоковій системі змішування;
- швидке змішування (3 - 10 хв.)
- зручне підмішування компонентів через спеціальну воронку;
- оглядові вікна по всій висоті змішувача, для візуального контролю;
- високоточні вагові датчики;
- масляний насос зі шлангами і переходами, для подачі в змішувач масляних компонентів
Лінія може бути укомплектована ділянкою приготування преміксів.
- в нього входить власний горизонтальний змішувач 300-500 кг, встановлений на вагові датчики з текстовим дисплеєм;
- бункери для зберігання компонентів і готових преміксів;
- шнеки подачі і вивантаження.
4. Ділянка готового корму
- Проектування ділянки готової продукції відповідно вимогами замовника!
- Комплектується сховищами готового корму відповідно до необхідним обсягом запасу готового корму і транспортує обладнанням необхідної продуктивності.
- При використанні додаткового вагового обладнання можливе відвантаження кормів з точністю до 1 кг.
Таким чином відпадає необхідність додаткового зважування кормораздавача або іншого транспортного засобу, який здійснює доставку корму споживачеві.
Етапи процесу виробництва комбінованого корму.
Приймання сировини (рис 3.2)
При надходженні сировини, отримують посвідчення про якість продукту, та зробивши аналіз, дають висновок про придатність його для використання у виробництві та дозвіл на розвантаження. Проводиться контроль по розвантаженню та правильність розміщення сировини для зберігання в бункерах.
Сировина, що поступає фасована в мішках розміщується для зберігання на піддонах в два яруси на складі. Мучниста сировина поступає автотранспортом, розвантажується з допомогою автомобілерозвантажувача У-АРГ-16У1 та ланцюгом транспортних механізмів ( ТЛ та норій) потрапляє в бункера СМС.
Жир тваринного та рослинного походження постачається автоцистернами та з допомогою шестерінчастих насосів подається до складських резервуарів, або витратних у виробничому приміщенні.
Борошно вапняку постачається на комбікормовий завод залізничними вагонами та пройшовши вхідний контроль розвантажується з допомогою транспортної лінії в бункера дозування.
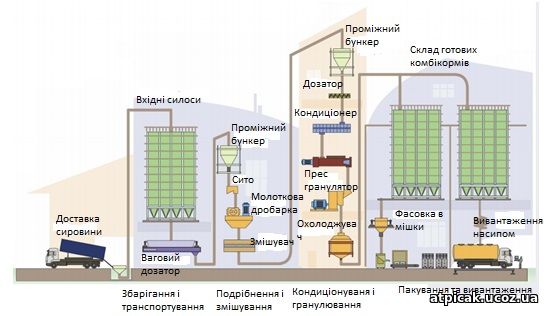
Рисунок 3.2 - Схема виробництва комбікорму
Дозування та змішування
Отримавши завдання на виробництво комбікорму оператор розпочинає роботу з перевірки правильності запрограмованих компонентів згідно рецепту, розробленого програмою і переданого в програму виробництва, та візуально перевіряє правильність дозування:
а) макрокомпонентів;
б) мінеральних компонентів;
в) мікрокомпонентів.
На початку та в процесі виробництва проводить завантаження сировини в бункера дозування:
а) зернової та мучнистої сировини – із складу СМС, автоприйому та елеваторів;
б) мінеральної сировини – залізної дороги та складу підлогового типу;
в) мікрокомпонентів- складу підлогового типу;
г) тваринного та рослинного жирів – витратні резервуари виробничого приміщення;
Дозовані компоненти транспортними лініями потрапляють в бункер над змішувачем, компоненти зернової та мучнистої сировини попередньо подрібнюються на молоткових дробарках ОРТІ -1200, з ситовим полотном Ø 3мм. Після того, як всі дозовані компоненти потрапили в бункер над змішувачем, відбувається завантаження змішувача, а далі процес змішування компонентів на змішувачі горизонтального типу НРВ-10000. Контроль часу змішування дозованих компонентів проводить оператор, фіксуючи час на секундомірі.
Під час змішування до суміші компонентів за допомогою дозуючих пристроїв додаються рідкі рослинні та тваринні жири.
Гранулювання
Змішана суміш потрапляє в бункер-змішувач над лінією гранулювання, попередньо пройшовши очистку від метало - магнітних домішок на магнітному сепараторі. З бункера, за допомогою живильника, суміш потрапляє на кондиціювання в кондиціонер СМ1101, де насичується паром з температурою в 140°С та тиском 2 Бари на протязі 45 секунд. Далі суміш потрапляє до експандера FEX42 де підлягає динамічним навантаженням з максимальною температурою 94°С. Після експандера продукт живильником-подрібнювачем подається на прес-гранулятор PM1219W та гранулюється шляхом продавлювання через матрицю з діаметром каналів 3 мм.
Гранульований продукт попадає через шлюзовий затвор до охолоджувальної колонки, де з допомогою вентиляційної системи зовнішнім повітрям охолоджується до температури на 10°С вищої від температури навколишнього середовища.
Охолоджений гранульований продукт просіюється на сепараторі, з якого дрібна та крупна фракції повертаються на гранулювання, а чиста гранульована маса проходить процес напилення на неї двох рідких ронозимів, на механізмі MFS із системою управління напиленням.
Після цього вже готовий сформований комбікорм проходить процес зважування на автоматичних вагах та по транспортному ланцюгу потрапляє на склад готової продукції у відповідний бункер, що запрограмований на певний вид комбікорму.
Видача готової продукції
Завантаження комбікорму здійснюється на автотранспорт та залізничні вагони. На протязі всього завантаження відбираються проби та формують зразок для проведення технічного аналізу якості завантаженого комбікорму. Проводить аналіз завантаженого комбікорму та при позитивному результаті аналізу дає дозвіл на відправку на зважування.
Система управління виробництвом комбікормів призначена для автоматизації управління всім технологічним обладнанням комбікормового заводу або цеху і забезпечує:
- управління технологічним обладнанням комбікормового заводу, складу зберігання, шляхами подачі вихідних компонентів і видачі готової продукції комбікормового виробництва;
- однокомпонентних і багатокомпонентних ваг (дозаторів) з похибкою дозування вихідних компонент ± 0,1% за рахунок автоматичної адаптації системи до параметрів обладнання і стану компонентів;
- введення загальної, для всього заводу, заявки на приготування комбікорму за заданим рецептом і перерахунок складу і маси компонентів для кожного дозатора;
- незалежний пуск і робота дозуючих підсистем з різними рецептами виробництва комбікормів;
- завантаження змішувачів кормовою сумішшю або вихідними компонентами по заданому рецепту і перемішування суміші в часі;
- управління процесами дроблення і екструдування зерна шляхом регулювання подачі зерна або інших компонентів, в залежності від навантаження на електропривод;
- контроль роботи і діагностика несправностей технологічного обладнання заводу комбікормів, локалізація несправностей;
- включення необхідних технологічних маршрутів виробництва комбікормів для створення транспортних шляхів подачі потоку вихідних компонентів на переробку і видачу готових комбікормових сумішей на силос зберігання або силос видачі;
- аналіз потоків вихідних компонентів виробництва комбікормів і регулювання їх подачі, що виключає перевантаження транспортних шляхів, холостий пробіг обладнання, забезпечує безперервність потоку компонентів;
- автоматична настройка системи управління на вимірювання параметрів технологічного агрегату внаслідок його ремонту або заміни;
- автоматизований облік приготованих комбікормових сумішей (за рецептами, за назвами і датами) і витрати вихідних компонентів з видачею встановлених форм в бухгалтерію та відділ збуту;
- ведення протоколу дій персоналу;
- ведення протоколу аварійних ситуацій і подій;
- облік мотогодин по кожного технологічного агрегату;
- контроль аварійних ситуацій, спрацьовування блокувань і захистів;
- захист не розвантаженого або несправного змішувача;
- оперативне відображення інформації про виробництво комбікормів і протікання процесів (рис 3.3), основні параметри роботи найбільш енергоємного обладнання на екрані моніторів операторських станцій.
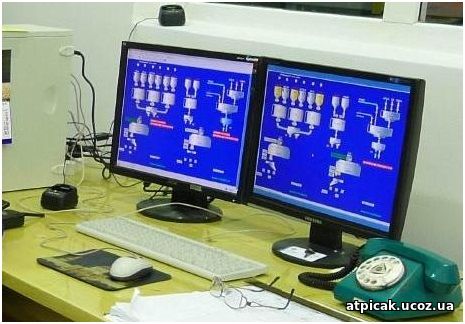
Рисунок 3.3. АРМ чергового оператора
При необхідності до АСУ ТП виробництва комбікормів можуть бути підключені:
система зважування на автомобільних і залізничних вагах;
система термометрії.
АСУ ТП заводу з виробництва комбікормів може бути інтегрована в локальну обчислювальну мережу підприємства або об'єднання. Доступ до інформації системи може здійснюватися через Інтернет або за допомогою мобільного телефону стандарту GSM.
Особливості реалізації системи управління виробництва комбікормів:
- для запуску виконання заявки на виробництво комбікормів оператору досить ввести необхідний рецепт і обсяг готової суміші. Контроль допустимості параметрів заявки, наявності необхідних за рецептом компонентів, поділ на типи визначається автоматично;
- для створення і запуску необхідних транспортних шляхів, оператору досить вказати номер потрібного маршруту;
- при виявленні аварійних ситуацій на одному з технологічних маршрутів, виконання поточної заявки на приготування кормової суміші або подача вихідних компонент для даної підсистеми припиняється, обладнання технологічного маршруту вимикається за заданим алгоритмом, оператору-технологу на екран монітора видається повідомлення про аварійну ситуацію (дубльоване голосовим повідомленням з динаміка комп'ютера) із зазначенням причини, що призвела до зупинки технологічного ланцюжка;
- малі похибки дозування досягаються за рахунок застосування автоматичної адаптації до затримок спрацьовування затворів і швидкостям закінчення матеріалів, застосування методів обробки тензосигналів в умовах впливу вібрацій;
- скорочення часу виконання заявки виходить за рахунок максимального розпаралелювання та суміщення технологічних операцій;
- зв'язок з оператором забезпечує доступ персоналу до ресурсів системи за допомогою панелей управління, зображених на екранах моніторів, клавіатури і маніпулятора типу «миша»;
- панелі управління відображають стан елементів системи і всіх технологічних процесів (рис 3.4.), а також дозволяють викликати: вікна введення заявок і рецептів, мнемосхеми, суміщеними з панелями управління окремими технологічними процесами, журнали з нормативно-довідкової і обліковою інформацією, журнали з настроювальними параметрами системи управління, додаткові індикатори стану найбільш важливих елементів системи управління.
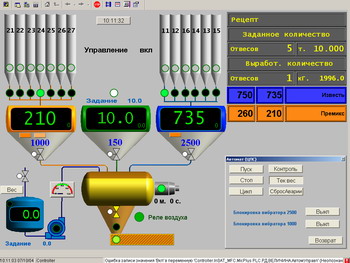
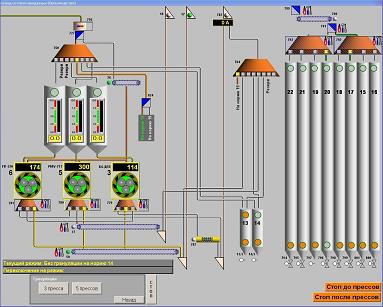
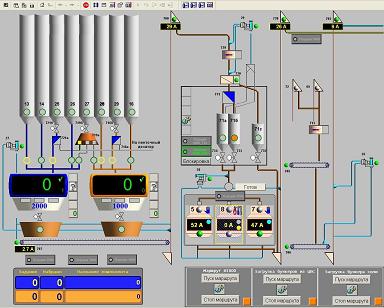
Рисунок 3.4. Відображення стану елементів системи і всіх технологічних процесів приготування на екрані монітору
Комплект обладнання для автоматизації комбікормового заводу
- операторські станції АСУ ТП (офісні або промислові комп'ютери), встановлені на робочих місцях операторів підприємства;
- сервер;
- технологічні контролери, встановлені безпосередньо в цехах, в складі: базовий блок, що містить IBM-сумісний процесорний модуль, мережева плата Ethernet, модулі оптоізолірованного введення-виведення цифрових і аналогових сигналів;
- шафи або панелі з електрообладнанням, захисною апаратурою і клемники;
- безконтактні датчики положення і руху виконавчих механізмів;
- датчики критичного верхнього і нижнього рівня силосів зберігання і наддозаторних бункерів, підпору технологічного обладнання;
- тензометричні канали вимірювання ваги;
- датчики струмового навантаження технологічних агрегатів;
- кабельна мережа
Економічна ефективність
Впровадження системи дозволяє досягти максимальної продуктивності підприємства, необхідної якості приготування сумішей, економії матеріалів без заміни існуючого технологічного обладнання.
Основний економічний ефект від застосування системи виходить за рахунок скорочення витрат компонент в результаті підвищення точності дозування в зоні негативних допусків СНиП, за рахунок зменшення часу холостий роботи обладнання, за рахунок скорочення персоналу.
Використані матеріали http://insat.ru/, https://studfiles.net/
|