АВТОМАТИЗАЦІЯ ОБКАТУВАННЯ АВТОТРАКТОРНИХ
ДВИГУНІВ
Обкатування — завершальна операція при ремонті двигунів
внутрішнього згоряння (ДВЗ).
Вона
забезпечує приробляння взаємно тертьових поверхонь деталей. У процесі
обкатування виявляються й усуваються дефекти, які знижують надійність ДВЗ в
експлуатації.
На
мотороремонтних підприємствах застосовують комбіноване потрійне обкатування:
холодну, гарячу холосту і гарячу під навантаженням.
При
холодному обкатуванні непрацюючий ДВЗ прокручують від електродвигуна на малих
оборотах: починаючи приблизно з 500 і закінчуючи при 1000...1400 хв-1.
При гарячим холостому обкатуванням ДВЗ працює на холостому ходу. Холосте
обкатування починається з закінчення холодної, коли ДВЗ надійно запускається, і
закінчується при 1400...1800 хв-1. Електродвигун у цьому режимі
відключений.
При
гарячому обкатуванні під навантаженням ДВЗ працює як первинний двигун, що
обертає гальмо чи той же електродвигун.
Електродвигун переводять у режим генератора. Вироблювана ним електроенергія
надходить у загальну електромережу. Навантажують ДВЗ
поступово, починаючи з 1600...1800 хв-1 і закінчуючи при 1700...2200
хв1.
Навантаження
змінюється ступінями від 10...20 до 85...100% номінальної потужності, що
обкатується ДВЗ. На цьому ж стенді ДВЗ випробовують для виявлення надійності
його роботи і визначення основних техніко-економічних показників.
Для
обкатування ДВЗ використовують стенди ГОСНІТІ з асинхронними електродвигунами
потужністю від 4,5 до 160 кВт частотою обертання від 750 до 1500 хв-1.
Електродвигуни використовують з контактними кільцями в ланцюзі ротора, до яких
приєднують рідинні реостати. Змінюючи глибину занурення електродів реостата в
рідину, регулюють частоту обертання в діапазоні 1...2,5.
Неширокий
діапазон регулювання частоти обертання і мимовільне її відхилення через зміну
опору реостата при електророзігріві рідини — істотні недоліки цих стендів.
Деякі
ремонтні майстерні і підприємства використовують автоматичні обкатувально
випробувальні стенди з асинхронно-вентильним каскадом (АВК) (рис. 8.7) потужністю
вище 60 кВт. Стенд містить кінематично з'єднаний з валом ДВЗ 3, що
обкатується, асинхронний електродвигун 1
з фазним ротором. Струми обмоток ротора випрямляються випрямлячами 22, 23 і 24,
інвертуються трифазним інвертором струму ІТ і через трансформатор, що узгоджує,
15 направляються в мережу. Завдяки наявності АВК у мережу повертається
(рекуперуєтся) до 80% енергії, що забирається стендом.
Для
автоматичного керування режимами обкатування стенд обладнаний відповідними
приладами: датчиками 2 крутного моменту, датчиком 4 швидкості зміни
температури, датчиками температури масла в системі змащення, датчиком частоти
обертання — тахометром 14, підсилювачами-перетворювачами 5, 6, 8 і 11,
органами, що порівнюють 10 і 7, задатчиками програми обкатування 9 і крутного
моменту, 13 і блоком 12 для фазоімпульсного керування групами вентилів 19, 20 і
21 інвертора струму ІТ. Трансформатор інвертора струму має трифазну
вторинну обмотку 15 і три секціонуванні первинні трифазні обмотки 16, 17 і 18.
Вторинні
обмотки 16 і 18 з'єднані за схемою «зиґзаґ», а обмотки 17 — за схемою «зірка» з
додатковою обмоткою, з'єднаної в «відкритий трикутник». Це поліпшує форму
кривої напруги на обмотці 15 і поліпшує узгодження рівнобіжної роботи інвертора
ІТ з мережею.
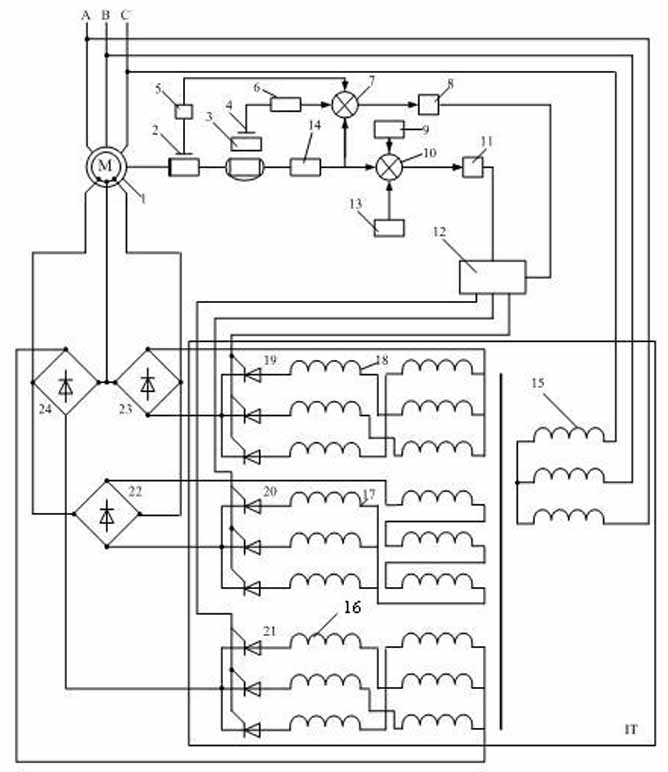
Рисунок. 8.7. Принципова електрична схема
обкатувально- випробувального стенда з АВК.
Задатчиками
9 та 13 задаються тимчасові програми наростання частоти обертання і гальмового
моменту при обкатуванні двигуна з урахуванням температури нагрівання масла. В
органах порівняння 10 та 7 відбувається порівняння фактичних величин частоти і
моменту обертання з заданими значеннями. За допомогою підсилювачів 5, 11, блоку
керування 12 інвертор струму ІТ відбувається відпрацьовування заданої програми
обкатування.
Перехід з одного режиму але наступний відбувається автоматично від
датчика 4 швидкості зміни температури
масла. Як тільки температура масла в системі змащення припиняє свій ріст, то
при холодному обкатуванні збільшується
на ступінь частота обертання, а при гарячої — гальмовий крутний момент.
При новій стабілізації температури виробляється сигнал для переходу на наступну
ступінь обкатування.
На великих моторобудівних підприємствах обкатувально-
випробувальні стенди мають програмне керування по 3...5 незалежних параметрах,
а також контроль і обробку на микро - ЕОМ техніко-експлуатаційних параметрів
ДВЗ при обкатуванні з висновком результатів на цифродрук і видачею даних на ЕОМ
підприємства.
На моторобудівних і мотороремонтних підприємствах
застосовують автоматизовані комплекси для обкатки і випробування ДВЗ. На
цих комплексах відбувається програмне управління обкаткою по двох—п'яти
незалежних параметрах, випробування ДВЗ на нестійких режимах,
контроль і обробка на ЕОМ параметрів двигунів при обкатці з висновком
результатів на друк. Всі обкатувально-випробувальні стенди оснащені, як
правило, дворівневою системою управління, причому кожен стенд забезпечений
мікроЕОМ, що управляє роботою ДВЗ і стенду. Крім того, мікроЕОМ, або мікропроцесори,
забезпечують захист ДВЗ і стенду від аварійних режимів роботи, збір, обробку і
протоколювання результатів вимірювань, а також видають необхідні дані в
управляючу обчислювальну машину.
Окрім пристроїв програмного управління представляють
інтерес експериментальні зразки пристроїв управління часом обкатки залежно від
швидкості зміни технічних параметрів і пристрою управління режимами обкатки
залежно від значення цих параметрів. Дані пристрої за певних умов можуть
забезпечити оптимальне прироблення поверхонь деталей обкачуваного, що труться, ДВЗ,
причому час обкатки визначається індивідуально для кожного двигуна.
Прироблення контактуємих поверхонь деталей супроводжується посиленим тертям і зносом. У міру
прироблення деталей тертя і знос знижуються, а після закінчення прироблення —
стабілізуються. Зміна тертя і зносу в часі супроводжується відповідною зміною
температур поверхонь деталей, що труться. Показниками якості прироблення можуть
також служити зміни витоку повітря, що вводиться всередину циліндра на стадії
холодної обробки, питомої витрати палива і кількості газів, що прориваються в
картер двигуна на стадії гарячої обробки під навантаженням. Характер зміни цих
показників дозволяє оцінити якість прироблення поверхонь деталей, що труться,
при обкатці.
|